Imagine this: You're working in a bustling workshop, surrounded by the hum of machines and the rhythmic sound of metal being shaped. Suddenly, there's a loud crash, and someone nearby is injured. It's every machinist's nightmare—a lathe machine accident. But what causes these accidents, and more importantly, how can we prevent them? That's exactly what we're diving into today.
Lathe machine accidents are more common than you might think, and they often result in serious injuries or even fatalities. In this article, we'll explore everything you need to know about lathe machine accidents—from the causes and statistics to prevention strategies and safety tips. If you work with lathes or supervise a workshop, this is a must-read.
We'll also cover real-life examples, expert advice, and industry best practices to help you stay safe on the job. Whether you're a seasoned machinist or just starting out, understanding lathe machine safety is crucial for protecting yourself and your team.
Understanding Lathe Machine Accidents
What Exactly is a Lathe Machine Accident?
A lathe machine accident refers to any incident involving a lathe machine that results in injury, damage, or loss. These machines, while incredibly useful for shaping metals and other materials, can be dangerous if not handled properly. Common injuries include cuts, burns, fractures, and even amputations.
Think about it—lathes spin at high speeds, and when something goes wrong, it can happen in the blink of an eye. Workers might get their hands caught in the machinery, or flying debris could cause serious harm. It's not just about the machine itself; human error and lack of proper training play a huge role too.
Common Causes of Lathe Machine Accidents
So, what exactly leads to these accidents? Let's break it down:
- Improper Training: Workers who haven't been properly trained on how to use a lathe machine are at higher risk of accidents.
- Ignoring Safety Protocols: Skipping safety checks or not wearing protective gear can have disastrous consequences.
- Machine Malfunctions: Even the best machines can break down, especially if they're not maintained regularly.
- Distracted Work: Trying to multitask or being distracted while operating a lathe can lead to serious mistakes.
These are just a few of the many factors that contribute to lathe machine accidents. By understanding the causes, we can take steps to prevent them.
Lathe Machine Accident Statistics
The Numbers Don't Lie
According to the Occupational Safety and Health Administration (OSHA), machine-related accidents account for a significant percentage of workplace injuries each year. Specifically, lathe machine accidents make up a notable portion of these incidents.
Here are some alarming statistics:
- Approximately 18,000 machine-related injuries occur annually in the U.S. alone.
- Lathe machines are responsible for around 10% of all machining injuries.
- Over 50% of lathe machine accidents involve workers who have less than one year of experience.
These numbers highlight the importance of proper training and safety measures. It's not just about protecting workers—it's about saving lives.
Preventing Lathe Machine Accidents
Training and Education
One of the most effective ways to prevent lathe machine accidents is through comprehensive training. Workers should be thoroughly trained on how to operate the machine, understand its limitations, and recognize potential hazards.
Training programs should include:
- Hands-on practice with experienced instructors.
- Regular refresher courses to keep skills sharp.
- Emphasis on safety protocols and emergency procedures.
Remember, knowledge is power. The more workers know about lathe machines, the safer they'll be.
Wearing the Right Gear
Protective gear might not seem like a big deal, but it can make all the difference in an accident. Workers should always wear:
- Safety goggles to protect their eyes from flying debris.
- Gloves to prevent cuts and burns.
- Steel-toed boots to protect their feet from heavy objects.
It might feel uncomfortable at first, but trust us—it's worth it. Think of it as an investment in your safety.
Best Practices for Lathe Machine Safety
Regular Maintenance
Just like your car, lathe machines need regular maintenance to function properly. Neglecting maintenance can lead to malfunctions, which in turn can cause accidents.
Here are some maintenance tips:
- Inspect the machine before each use to ensure everything is in working order.
- Keep the machine clean and free of debris.
- Replace worn-out parts promptly.
By keeping your lathe machine in top condition, you're reducing the risk of accidents significantly.
Following Safety Protocols
Safety protocols exist for a reason—to keep you safe. Here are some protocols you should follow:
- Never leave the machine unattended while it's running.
- Always double-check your settings before starting the machine.
- Keep your workspace organized and free of clutter.
These might seem like common sense, but you'd be surprised how often they're overlooked.
Real-Life Examples of Lathe Machine Accidents
Case Study: The Cost of Negligence
In 2019, a machinist in Ohio suffered a severe hand injury when he failed to follow safety protocols while operating a lathe machine. He was distracted by a phone call and didn't notice that his hand was too close to the spinning blade. The result? A trip to the emergency room and several months of recovery.
This case highlights the importance of staying focused and adhering to safety guidelines. It's a reminder that even a momentary lapse in attention can have serious consequences.
Learning from Mistakes
Another incident occurred in a factory in Michigan, where a lathe machine malfunctioned due to lack of maintenance. The machine overheated, causing a fire that spread quickly through the workshop. Thankfully, no one was injured, but the damage was extensive.
These examples serve as a wake-up call for all of us. By learning from others' mistakes, we can prevent similar incidents from happening in the future.
Industry Best Practices
Adopting a Safety Culture
Creating a culture of safety in your workplace is essential for preventing lathe machine accidents. This involves:
- Encouraging open communication about safety concerns.
- Rewarding workers who follow safety protocols consistently.
- Providing regular safety training and updates.
When everyone is on board with prioritizing safety, the risk of accidents decreases dramatically.
Technology and Innovation
Advancements in technology have made it easier to prevent lathe machine accidents. Modern machines come equipped with safety features like automatic shut-offs and sensors that detect potential hazards.
Incorporating these technologies into your workshop can significantly reduce the risk of accidents. It's all about staying ahead of the curve and using the tools available to you.
Conclusion
Lathe machine accidents are serious business, but they're also preventable. By understanding the causes, following safety protocols, and staying informed, we can create safer workplaces for everyone.
So, what can you do next? Start by reviewing your current safety practices and identifying areas for improvement. Encourage your team to speak up about any concerns they might have. And most importantly, never stop learning. The more you know, the safer you'll be.
We'd love to hear from you! Share your thoughts in the comments below or check out our other articles for more tips on workplace safety. Together, we can make a difference.
Table of Contents
- Understanding Lathe Machine Accidents
- Common Causes of Lathe Machine Accidents
- Lathe Machine Accident Statistics
- Preventing Lathe Machine Accidents
- Training and Education
- Wearing the Right Gear
- Best Practices for Lathe Machine Safety
- Regular Maintenance
- Following Safety Protocols
- Real-Life Examples of Lathe Machine Accidents
- Industry Best Practices
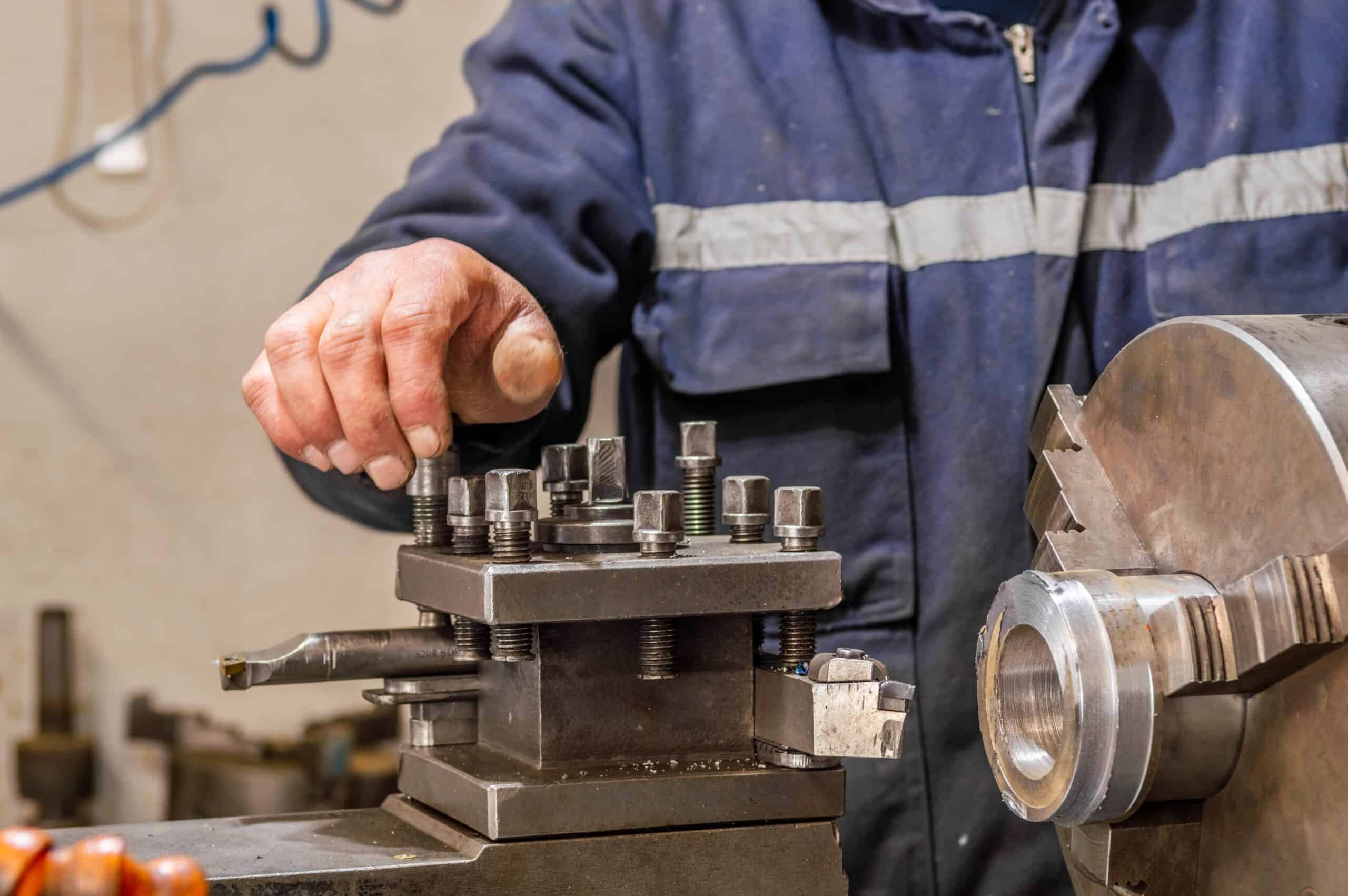
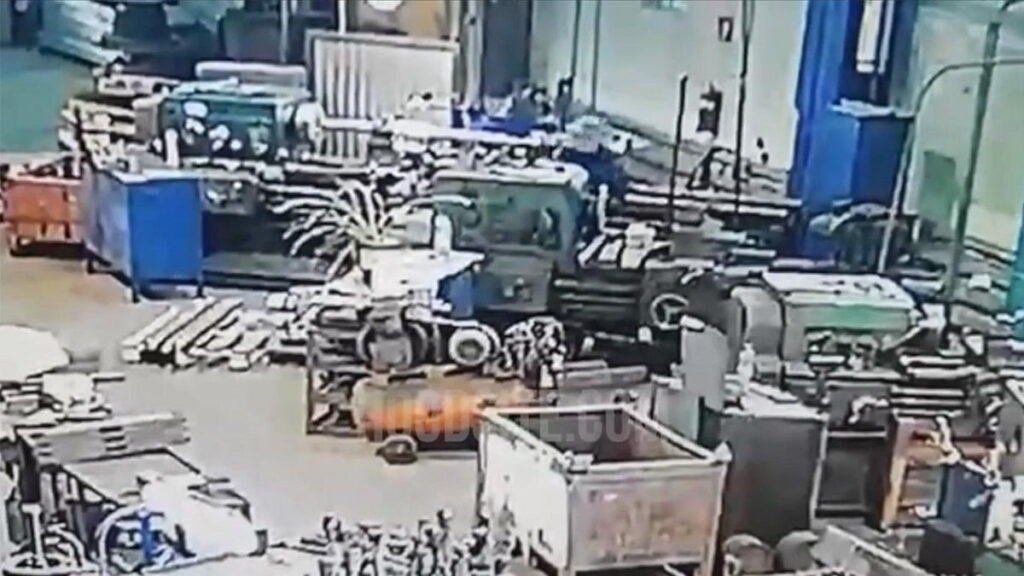
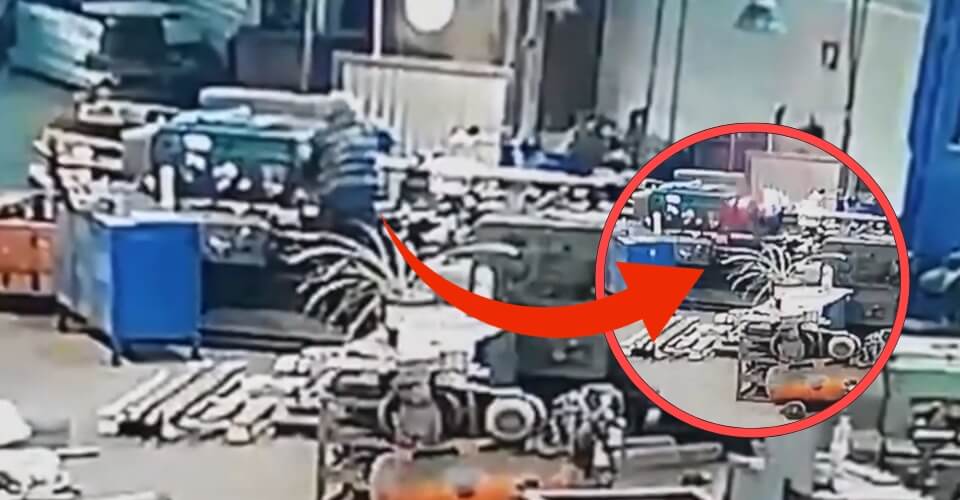